CSIR-CIMFR Conducts First Trial Blast of Dozer Push Mining Method, Revolutionizing Indian Mining Practices
The Dozer Push Mining Method, developed as part of a two-year scientific study by CSIR-CIMFR, focuses on deep-hole cast blasting at PEKB Opencast Coal Mine.
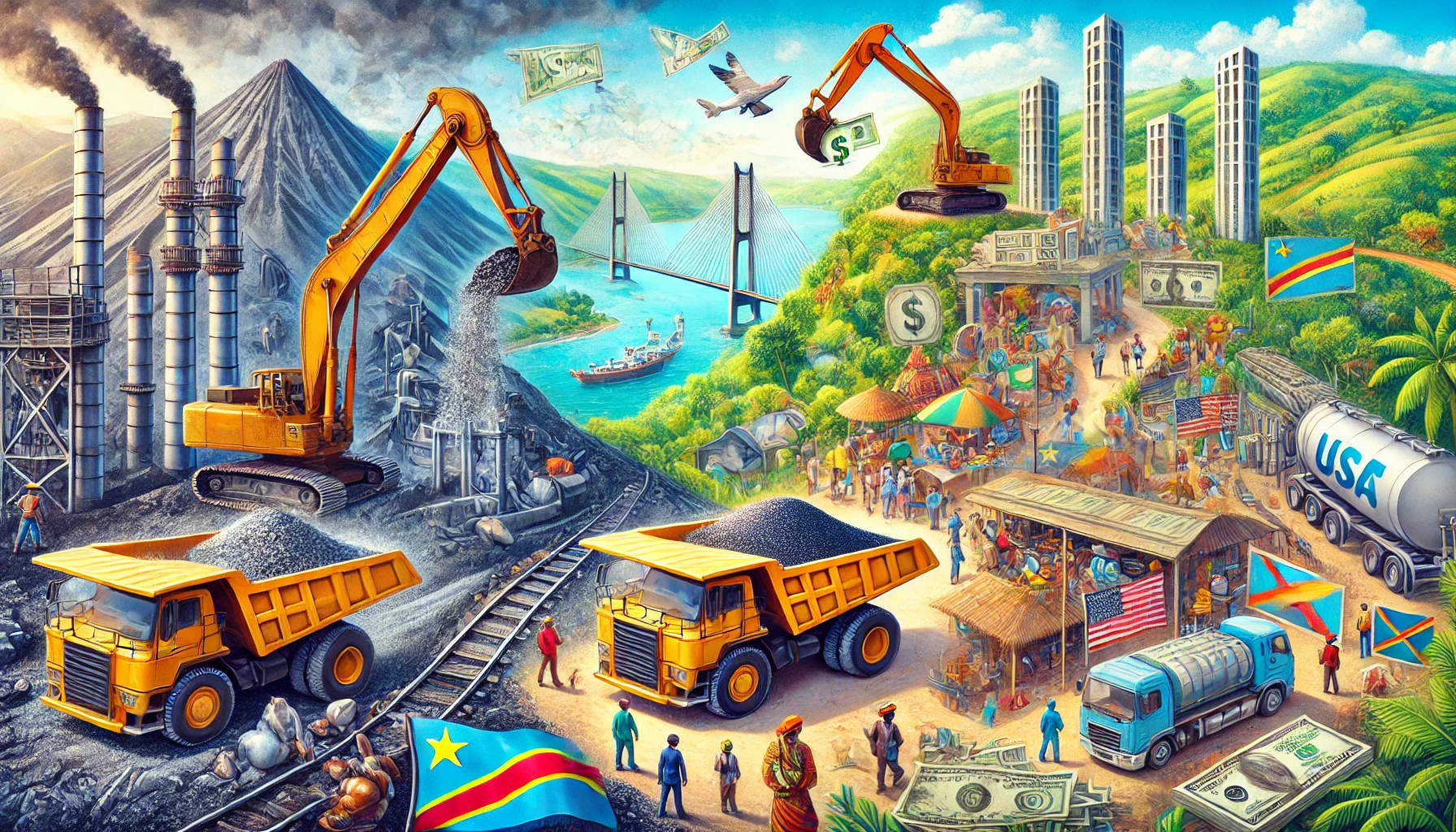
- Country:
- India
In a landmark development for India's mining industry, the CSIR-Central Institute of Mining and Fuel Research (CSIR-CIMFR) has successfully conducted the first trial blast using the Dozer Push Mining Method integrated with advanced digital technologies. This pioneering initiative, conducted at the PEKB (Parsa East and Kanta Basan) Coal Mine in the Udaipur block of Ambikapur, Chhattisgarh, introduces a groundbreaking, automated approach to mining operations, aimed at enhancing safety, efficiency, and cost-effectiveness.
The trial was carried out in collaboration with Adani Natural Resources, a leading private mining company in India. This innovative method represents a paradigm shift in mining technology, emphasizing automation, reduced environmental impact, and improved worker safety.
A Game-Changing Mining Method
The Dozer Push Mining Method, developed as part of a two-year scientific study by CSIR-CIMFR, focuses on deep-hole cast blasting at PEKB Opencast Coal Mine. The trial involved drilling 108 holes with unmanned, automated drill machines, followed by cast blasting using 60 tons of bulk emulsion explosives. The blasted material was then efficiently pushed into the decoaled area using large, automated dozer machines designed specifically for this purpose.
Advantages of Dozer Push Mining Method:
- Cost Efficiency: Estimated to reduce operational costs by 7–10% compared to conventional methods such as truck-shovel or dragline techniques.
- Safety: Unmanned operations significantly minimize the risks associated with traditional mining techniques.
- Environmental Impact: Controlled detonation and material handling reduce vibrations and flyrock, adhering to strict environmental standards.
- Operational Efficiency: Faster coal recovery and the ability to maintain productivity during adverse weather conditions, such as monsoons.
- Enhanced Productivity: Optimized use of dragline machines and other resources, reducing unit costs.
Technical Excellence and Leadership
The trial was spearheaded by Prof. Arvind Kumar Mishra, Director of CSIR-CIMFR, and a team of scientists and engineers, including Dr. Murari P. Roy, Dr. Vivek K. Himanshu, Mr. R. S. Yadav, Mr. Suraj Kumar, and Dr. Ashish K. Vishwakarma. The team demonstrated precise drilling, safe blasting, and efficient material movement, showcasing the method's viability for large-scale application.
Next Steps in Implementation
The first phase of the trial showcased the potential of this method to transform mining operations. The second phase will involve conducting 8–10 additional trial blasts to further refine the design and operational parameters. These trials aim to optimize the Dozer Push Mining Method for broader adoption across Indian coal mines.
Significance for the Indian Mining Sector
This breakthrough aligns with India's vision to modernize its mining sector by integrating cutting-edge technology and reducing dependence on conventional methods. The implementation of the Dozer Push Mining Method highlights the potential for automation and innovation to improve productivity, ensure safety, and minimize environmental impact.
With this achievement, CSIR-CIMFR and its collaborators have set a benchmark for technological advancements in mining, marking a step forward in India’s journey toward sustainable and efficient mining practices. The initiative not only revolutionizes mining methodologies but also sets a global example of integrating science and technology for industrial transformation.