How PLC works in industry?
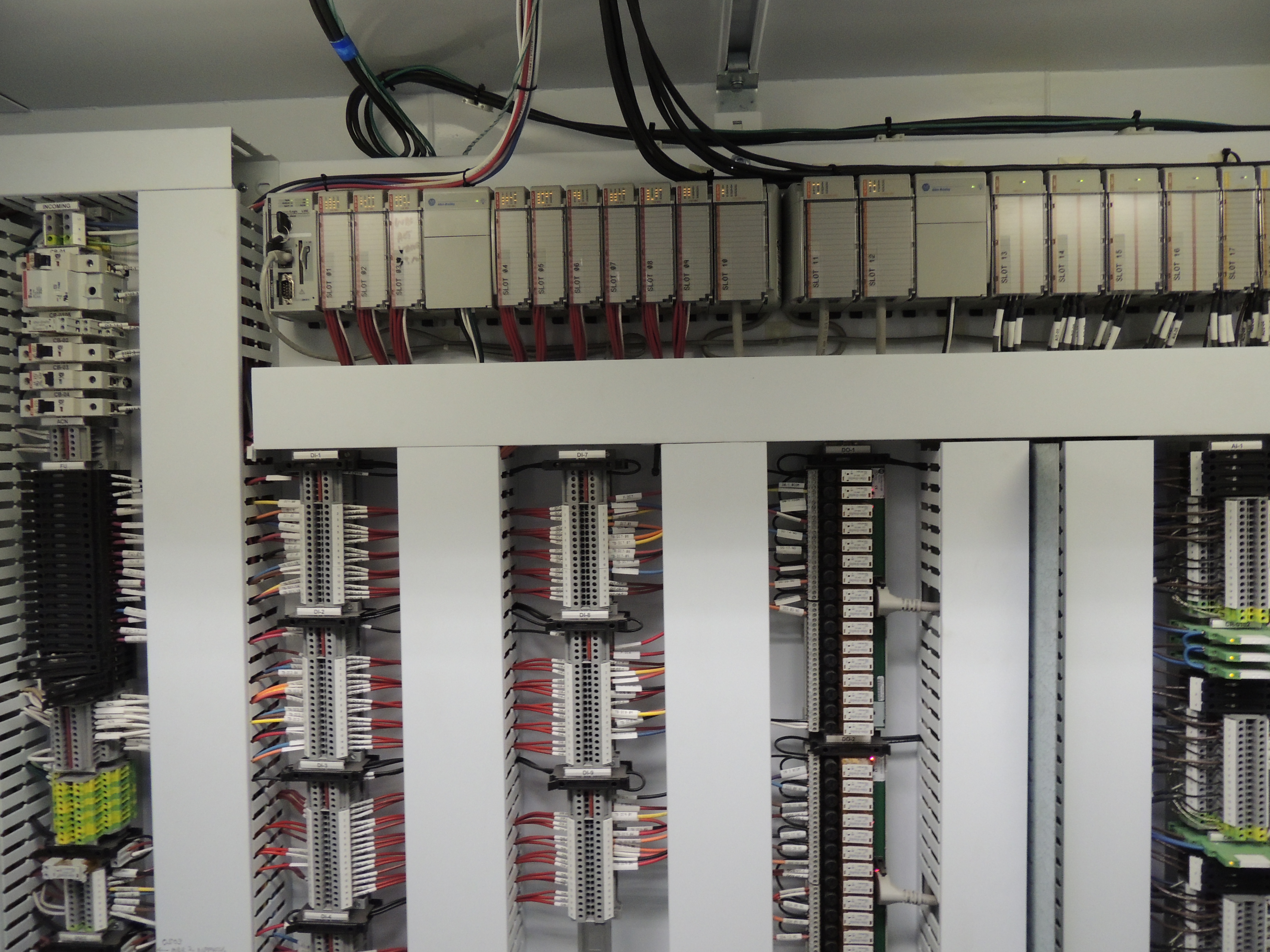
Explore the remarkable evolution and essentiality of Programmable Logic Controllers (PLCs) in today's industrial landscape. Delve into the transformative journey of PLCs since their emergence in the 1970s, witnessing their pivotal role in revolutionizing manufacturing processes and machinery control. From humble beginnings to indispensable industrial automation components, PLCs have seamlessly integrated into various sectors, driving efficiency, precision, and innovation. Join us as we unravel the intricate tale of PLCs and their profound impact on modern industrial practices.
What is PLC?
Uncover the essence and importance of Programmable Logic Controllers (PLCs) as dedicated digital computing systems engineered for industrial process management. Grasp their critical function in executing logical operations on input data to oversee electromechanical procedures spanning diverse industries. Gain insight into how PLCs serve as the central nervous system of industrial automation, orchestrating intricate tasks with precision and efficiency.
PLCs are the cornerstone of modern industrial automation, offering a sophisticated blend of computational power and real-time control. These specialized digital computers are meticulously designed to handle industrial environments' complex and dynamic demands, where precise control and reliability are paramount. By harnessing their logical processing capabilities, PLCs empower industries to streamline operations, enhance productivity, and ensure the seamless functioning of machinery and processes.
PLCs serve as the nerve center of industrial automation, seamlessly integrating with sensors, actuators, and other control devices to orchestrate a symphony of operations. From manufacturing plants to power generation facilities, PLCs are pivotal in optimizing processes, minimizing downtime, and maximizing efficiency. Understanding PLCs' fundamental principles and functionalities is essential for professionals working in automation and control systems, enabling them to design, deploy, and maintain robust and efficient industrial automation solutions.
The PLC Process
The PLC process unfolds as a meticulously orchestrated symphony of digital logic, seamlessly blending input signals, logical operations, and output control to drive industrial automation forward. At its core, a PLC serves as the central nervous system of a manufacturing or industrial process, adeptly processing sensory inputs and issuing precise commands to actuators and machines.
To grasp the essence of the PLC process, one must first understand its role in converting raw sensory data into actionable commands. PLCs serve as the bridge between the physical world of sensors and the digital realm of control logic, interpreting input signals from sensors and executing programmed instructions based on predefined logic.
At the heart of the PLC process lies its ability to adapt to diverse application needs through configurable input and output ports. These ports serve as the conduits through which sensory data flows into the PLC and control signals flow out, allowing seamless integration with a wide array of sensors, actuators, and other control devices.
From monitoring temperature and pressure sensors to regulating motor speed and conveyor belt operations, PLCs excel in orchestrating complex sequences of operations with precision and efficiency. PLCs can accommodate many application requirements by leveraging configurable input and output ports, offering unparalleled flexibility and scalability in industrial automation settings.
The PLC process embodies the seamless convergence of sensory inputs, logical operations, and precise control, culminating in the synchronized orchestration of industrial machinery and processes. This inherent adaptability and versatility make PLCs indispensable assets in modern industrial automation, driving efficiency, productivity, and innovation across various sectors and applications.
Components of a PLC System
Delving into the inner workings of a PLC system unveils a sophisticated interplay of essential components, each meticulously engineered to ensure the seamless orchestration of industrial automation processes. Understanding these components is paramount to grasping the holistic functionality of PLC-based solutions and their pivotal role in modern industrial settings.
Power Supply:
The power supply unit is at the core of every PLC system, serving as the lifeblood that energizes the entire system. The power supply ensures uninterrupted operation and reliability. It is responsible for converting external AC or DC power sources into the stable voltage levels required by the PLC components. Siemens, a leading PLC manufacturer, maintains a robust stock of power supply units, catering to diverse industrial requirements efficiently and reliably.
Processor:
The processor is the cerebral cortex of the PLC system, orchestrating the execution of programmed instructions and logic operations. Like a digital brain, the processor processes input data, executes control algorithms, and generates output signals with unparalleled precision and speed. Siemens PLCs boast cutting-edge processors engineered to deliver high-performance computing capabilities, enabling real-time responsiveness and seamless integration with industrial processes.
Communication Card:
Communication cards facilitate seamless communication between PLCs and external devices or networks and serve as the nerve center of data exchange in industrial automation systems. These cards enable PLCs to interact with supervisory control systems, human-machine interfaces (HMIs), and other devices via standard communication protocols such as Profibus, Profinet, or Ethernet/IP. Siemens stocks diverse communication cards, ensuring seamless integration and interoperability across various industrial environments.
Input Modules:
Input modules serve as the sensory receptors of the PLC system, capturing real-world data from external sensors, switches, or devices. These modules convert analog or digital signals from the input devices into binary data that the PLC processor can interpret and act upon. Siemens offers an extensive portfolio of input modules tailored to diverse application requirements, from simple digital inputs to high-precision analog input modules, enabling precise data acquisition and control.
Output Modules:
Completing the feedback loop, output modules translate the processed control signals from the PLC processor into actionable commands for actuators, valves, motors, or other output devices. By converting digital signals into analog or pulse-width modulation (PWM) signals, output modules exert precise control over industrial processes, ensuring optimal performance and efficiency. Siemens stocks a comprehensive array of output modules, catering to diverse output requirements with reliability and precision.
In essence, the harmonious integration of these essential components forms the backbone of a PLC system, enabling seamless automation of industrial processes with unparalleled precision, reliability, and efficiency. With Siemens PLCs at the helm, stocked with diverse components, industrial enterprises can unlock new frontiers of productivity and innovation in today's dynamic manufacturing landscape.
How PLC Operates
Delving into the operational intricacies of Programmable Logic Controllers (PLCs) unveils a world of digital orchestration akin to a computer-tailored specifically for industrial automation. Understanding how PLCs operate is fundamental to grasping their pivotal role in streamlining industrial processes with precision and efficiency.
CPU and Memory:
At the heart of every PLC lies its central processing unit (CPU), akin to the brain orchestrating its functions. The CPU executes the programmed logic stored in the PLC's memory, which can be either volatile or non-volatile, ensuring the continuity of operations even during power loss. This memory stores the instructions that dictate how the PLC responds to input signals and generates output signals, enabling seamless control over industrial processes.
Input/Output (I/O) Modules:
The operational prowess of PLCs extends beyond mere computation, with input/output (I/O) modules serving as the conduits through which they interact with the physical world. Input modules receive signals from sensors, switches, or other devices, translating them into digital data that the CPU can process. Conversely, output modules convert the processed control signals from the CPU into actionable commands for actuators, motors, or other output devices, shaping the physical manifestation of the PLC's logic.
Interpretation of Input Signals:
PLCs rely on many input signals from sensors and other devices to perceive the state of industrial processes. These signals, ranging from simple binary on/off inputs to analog temperature, pressure, or flow measurements, provide the PLC with real-time data on the operational environment. The PLC determines the appropriate course of action to maintain process stability and efficiency by interpreting these input signals according to the programmed logic.
Execution of Programmed Logic:
Armed with a wealth of input data, the PLC's CPU executes the programmed logic stored in its memory with unparalleled precision and speed. Typically defined using ladder logic or other programming languages, this logic dictates how the PLC responds to various input conditions, orchestrating the sequence of operations required to achieve desired process outcomes. Whether controlling conveyor belts, regulating temperature levels, or coordinating complex manufacturing processes, the PLC executes its programmed logic with unwavering accuracy.
Generation of Output Signals:
Upon processing input data and executing the programmed logic, the PLC generates output signals that command actuators, valves, motors, or other output devices to effect tangible changes in the industrial environment. These output signals, meticulously crafted based on the programmed logic, exert precise control over machinery and processes, ensuring optimal performance and adherence to desired operational parameters.
In essence, the operational mechanics of PLCs mirror those of a computer, albeit specialized for industrial automation. PLCs empower industrial enterprises to streamline processes, enhance efficiency, and adapt dynamically to evolving operational requirements with unparalleled precision and reliability by interpreting input signals, executing programmed logic, and generating output signals.
Bottom line
In conclusion, exploring the remarkable evolution and essentiality of Programmable Logic Controllers (PLCs) unveils their transformative journey since the 1970s, culminating in their pivotal role in revolutionizing modern industrial practices. From humble beginnings to indispensable industrial automation components, PLCs have seamlessly integrated into various sectors, driving efficiency, precision, and innovation.
Understanding PLCs as dedicated digital computing systems engineered for industrial process management is paramount. They serve as the central nervous system of industrial automation, orchestrating intricate tasks precisely and efficiently. PLCs are the cornerstone of modern industrial automation, offering a sophisticated blend of computational power and real-time control to streamline operations, enhance productivity, and ensure the seamless functioning of machinery and processes.
The PLC process unfolds as a meticulously orchestrated symphony of digital logic, seamlessly blending input signals, logical operations, and output control to drive industrial automation forward. By adapting to diverse application needs through configurable input and output ports, PLCs accommodate many requirements with unparalleled flexibility and scalability.
(Devdiscourse's journalists were not involved in the production of this article. The facts and opinions appearing in the article do not reflect the views of Devdiscourse and Devdiscourse does not claim any responsibility for the same.)