Best Practices for Effective BOM Management
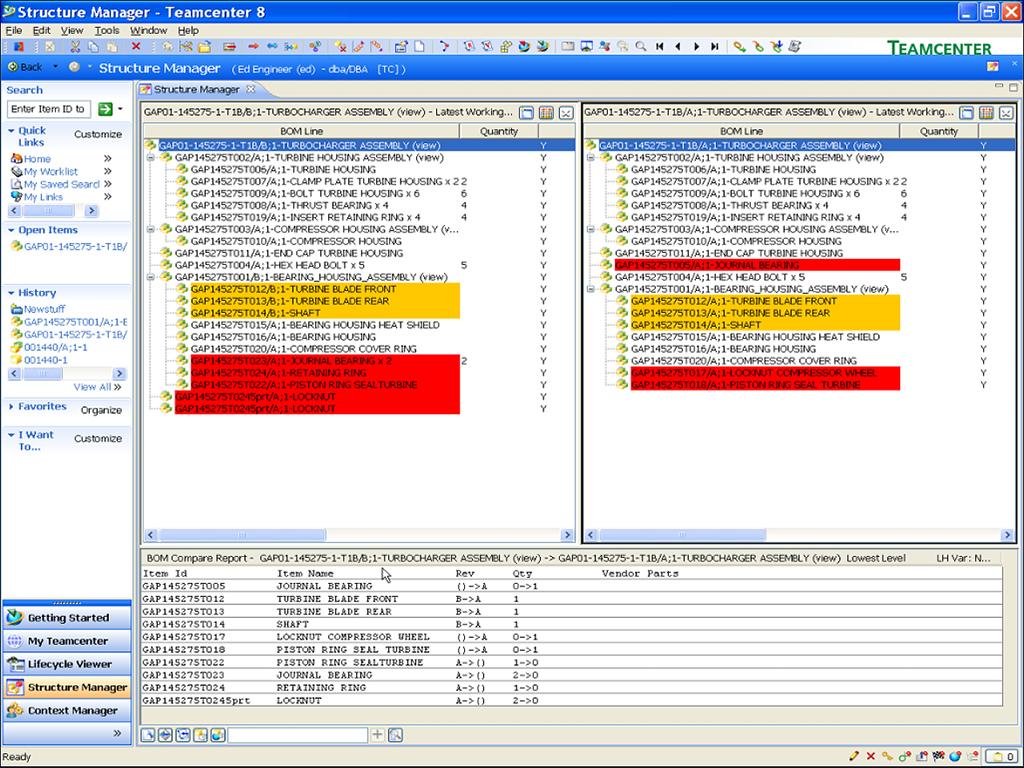
The bill of materials (BOM) is a comprehensive list of all the materials required to manufacture a product. Typically, this list includes raw materials, standard components, assemblies, sub-assemblies, and the quantities of each item. This makes BOM an important element of any manufacturing process as it assists a company in organizing its supply chain and material requirements, as well as planning and monitoring the production process.
The BOM is considered the recipe of a product, which makes it important to keep it as accurate and up-to-date as possible. A cake without sugar is a big disappointment. And a brake assembly with some parts missing is a big safety concern. This makes BOM management essential to connecting purchasing, design, and production in a manufacturing business. Moreover, an ineffective BOM process can lead to low productivity and costly errors that waste company resources and time.
With that said, why do many companies rely on substandard BOM management practices like email and spreadsheets? Is there a better way for manufacturing companies to manage BOM? This post will discuss some of the best practices for effective BOM management. Read on for more information.
Share BOM in Time
One of the most important things in BOM management is staying on the same page with all the involved parties. And the essential part is ensuring that all key stakeholders are involved in time. Thus, you should start doing this as early as possible—especially during the design phase. This will ensure that all the critical elements of the product design are analyzed by the supply chain, manufacturing, and other departments. Besides, this will help you identify procurement types and long lead times and engage different people and departments during this process.
Avoid Using Spreadsheets
Changes are a common thing in product development. And considering the number of acronyms used in any production process, change orders and designing go hand in hand. This brings forth one question—how can you keep your bill of materials current with so much change? And what if your BOM could reflect these changes automatically as they happen? The good news is that it's possible.
Instead of managing your spreadsheets manually, you should consider creating your BOM in the same product data management system you use to manage your production data. Also, you can use revision control to ensure that everyone is using the correct version and that any change is synced to your BOM automatically. Doing that ensures that your bill of materials is up-to-date with the latest development data and product design.
Centralize Your BOM
Since the manufacturing and design teams use numerous systems specific to their jobs’ roles, it’s essential to have a way of aggregating your product record into one system for better collaboration. With a centralized BOM, you get better control of the production process while streamlining the connection between the development team and product information to accelerate the development process.
Moreover, centralizing your BOM creates the required backbone for an effective manufacturing process by helping link all the related processes and product information. Also, this helps with change processes, like change orders, requests, and deviations, by connecting essential product record information. Lastly, it helps eliminate possible confusion by ensuring that teams have one place where they can create and make changes to the different product design features.
Automate Your BOM
A product life cycle has numerous stages and parts, requiring accurate and timely information sharing. This, however, cannot be possible if you use email or other conventional methods to share BOM information. These methods are time-consuming and prone to errors. And, as we mentioned above, there’s a high possibility of changes happening.
So, once you share BOM information via email, it can quickly become outdated. Besides, it’s important to consider the risk of contractors or suppliers using the wrong details to manufacture a product. Thus, it’s essential to reconsider the method that you use to share your bill of materials information. Should this method be faster, more accurate, and more effective? Yes! The advancement in technology has made it possible to have better methods of sharing your BOM information. Automating your BOM process ensures that other departments like manufacturing, procurement, quality control, and services can access the BOM. This also eliminates manual data entry, which can lead to costly mistakes.
Provide Secure Collaboration and Accountability
One thing you should never underestimate during a product lifecycle is accessing and sharing product information securely between external and internal teams. Most companies still use outdated collaboration methods, which don’t work well with highly dispersed production teams. Thus, it’s essential to make sure that access is easy for the users, secure, as well as quick to deliver and access.
Typically, you should start with certain restrictions and then allow specific access for external users to the BOM components they need to build or source materials. This is important as it ensures the integrity of the entire design and manufacturing process. In addition, it helps to reduce the risks of compromise from being shared with a wider audience. Moreover, manufacturing companies must ensure that audit trails are in place whenever a user accesses the product records. This helps to eliminate any possible ‘blame’ and increases accountability between the internal and external production teams.
Make Sure You Understand the Needs and Requirements of Your Production Team
It’s always important to sit down with your production team and ensure that you understand their requirements and needs throughout the product life cycle. However, you should be cautious to avoid evaluating the needs of one team—make sure that all the teams involved provide their input. This ensures that all needs and requirements are understood before the manufacturing process starts.
Product design, marketing, supply partners, quality control, and operations should be represented in the product development efforts. Please note that change might happen throughout your product lifecycle. Therefore, it’s important to make cross-functional collaboration your primary objective as the teams begin creating, sharing, importing, comparing, changing, and approving the items in your BOM.
Establish a Clear Flow of Information
One of the biggest enemies of BOM management is the lack of information flow. Therefore, it’s important to create effective communication channels between the parties involved to avoid the breakdown of important information. Please note that the more parties involved, the higher the risk of information breakdown. Thus, you should consider reducing the number of users in the BOM management lifecycle. You only need an admin and owner who oversee the contributor’s responsibility.
Also, limiting access ensures complete accountability of the people who make changes and mistakes. Moreover, you should consider integrating a change log, especially when choosing an automated process. A change log helps to track the details of changes in any category, as well as the user who initiated the change.
Moreover, you shouldn’t give editing authorization to anyone unless it’s important. Rather, users should only have read-only access. By restricting editing abilities, you reduce human error and prevent misinformed and accidental changes. Lastly, your BOM management should have a unique identifier code for anyone with editing permissions. This will ensure that queries about the details in the BOM are directed to the right person.
Don’t Ignore Risk Assessments
If your company manufactures complex products, you must collaborate with your supply chain partners to eliminate the risks of sourcing environmentally compliant and market-available components. Identifying and sourcing components that meet the required compliance is essential, as it helps reduce production costs and ensure that products are delivered on budget and on time. It is important to allow the right people to access compliance information and component lifecycle throughout your supply chain, as it ensures product quality and cost reduction and helps avoid any preventable shipping delays.
Bottom Line
Today’s BOM management process is a status quo—depending on outdated technology like email, and spreadsheets can lead to excess cost, inefficiency, errors, late orders, and quality issues. And the consequences of a flawed process can be significant, especially for small companies. Using BOM management software like PartAnalytics can help create a cohesive process that links everything from design to purchase orders and manufacturing. Moreover, it should allow users to access the correct information, which includes historical data, to resolve any service issues.
(Disclaimer: Devdiscourse's journalists were not involved in the production of this article. The facts and opinions appearing in the article do not reflect the views of Devdiscourse and Devdiscourse does not claim any responsibility for the same.)